By Kate Zuritsky | 03/07/2025
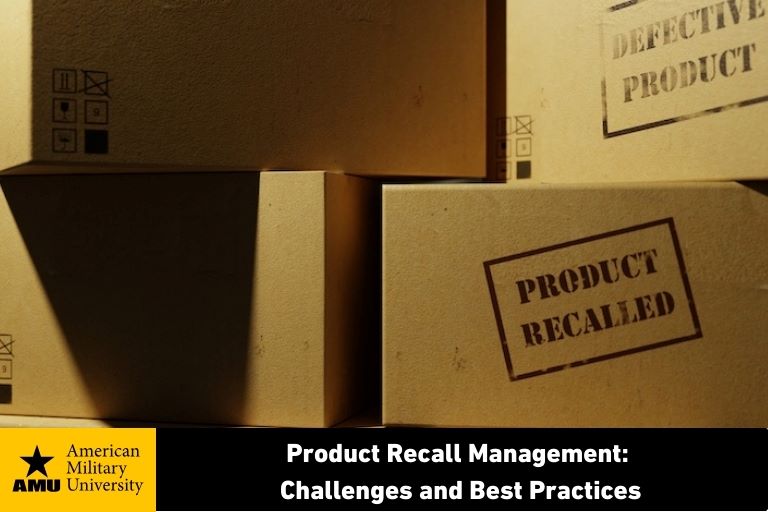
Product recalls are typically driven by various factors, such as complex global supply chains and tougher regulations. They are also increasing. According to the international insurance company Sedgwick, product recalls from U.S. companies soared to a five-year high in 2024.
During a product recall, organizations issue voluntary or mandatory recalls when there’s a potential hazard to the consumer. While a recall may initially cause panic and confusion, it mitigates risk for a company and protects people.
The high volume of recalled products suggests that there are weaknesses in supply chains. Organizations must implement product safety procedures to eliminate dangerous products from the market and adhere to product safety regulations.
What Is Product Recall Management?
Product recall management (PRM) is when a business identifies a problem and removes an unsafe product from the marketplace. A recall can happen for many reasons, including contamination, risk of fire, or a manufacturing defect that features serious safety concerns.
Government agencies like the Food and Drug Administration (FDA) and the Consumer Product Safety Commission (CPSC) help oversee recalls for:
- Food and drinks
- Consumer goods
- Pharmaceutical products
- Automotive products
- Medical equipment
- Agriculture products
Ideally, organizations must prepare an operational, legal, and public relations plan before a product becomes a safety issue.
The Role of the CPSC in Recalls
The Consumer Product Safety Commission (CPSC) created the Fast-Track Recall Program where business owners can report an unsafe product. The CPSC staff then evaluates the risk, decides if a recall is necessary, and works with a business to resolve the issue.
Additionally, the CPSC produced a recall handbook. This handbook outlines the product recall management process and the steps organizations must take to shield consumers from harm.
Product Recall Best Practices
If the safety of an item is questioned by your customers, the timing of your response is vital to retaining those customers. Be sure to quickly address the problem and evaluate whether the item needs a widespread recall. It’s critical to have a recall strategy in place before anything goes wrong.
The CPSC generated a process for conducting a recall. This process involves several important steps:
- Identify the issue
- Prepare a corrective action plan (CAP)
- Contact customers
- Remove the defective item
- Offer a solution
- Monitor recalled items
Identify the Issue
Does the product fail to comply with safety standards or is there a risk of injury or illness? Is there a supply chain issue?
Manufacturers, importers, and vendors should identify any problems with a defective item and then decide if a recall is warranted. Their ability to act quickly may significantly reduce health and safety risks to consumers.
Prepare a Corrective Action Plan
If a recall is necessary, your business and management must be prepared with a CAP to reduce the risk and prevent future problems. A CAP includes several components to ensure a recall is effectively communicated and managed.
It provides a complete roadmap for public recall notices and suggests changes to elements like design, materials, and quality control.
Contact Customers
After using the CAP, be sure to communicate to your customers and respond to any queries. Recall communications and public notices warn your customers of the increasing danger and encourage them to take action. Your CAP should include how customers can contact your business and your plans to reach out to media outlets and other channels.
Remove the Defective Item
Once you’ve implemented a CAP, it’s time to track your products and remove them from the marketplace. Your CAP should contain information like the types of communications or recall notices sent to customers, the number of items returned or repaired, and any post-recall incidents or deaths.
Offer a Solution
Company leaders should follow specific guidance in the CPSC’s handbook. They can decide whether a product should be replaced or repaired, or if customers should receive a refund.
Monitor Recalled Items
Your organization and the CPSC should monitor your recalled products. Organizations can use tracking tools, data, and reporting systems to ensure compliance with the Consumer Product Safety Improvement Act (CPSIA).
The Biggest Challenges Companies Face During a Recall
Recalls pose significant and expensive challenges to businesses, but organizations can learn from past recalls to strengthen safety protocols and improve risk management strategies. The biggest challenges in recall management include:
- Reputational damage – A recall can negatively impact customers’ views of your brand, leading to reputational damage and negative publicity.
- Financial impact – Shoppers may stop purchasing your products, leading to decreased sales. Also, consumer protection laws require suppliers and manufacturers to cover recall costs as well as the cost of government sanctions, lawsuits, and replacement products.
- Legal and regulatory issues – Product recalls have legal and regulatory implications. Customers who were harmed by your products may file lawsuits, and regulatory agencies might impose fines or penalties. Additionally, companies must work with authorities to remove the product from the market, report the issue, and ensure it doesn’t happen again.
- Supply chain disruptions – Recalls involve the need to locate and retrieve defective products from suppliers and retailers in the supply chain. These disruptions also slow down production and delivery and impact other products that need the same materials or product lines.
- Transportation complications – In addition to retrieving recalled products, companies must transport items from consumers and stores to their warehouses. If the products are dangerous or need specific storage space, specialized shipping and handling may be required.
Reverse Logistics Degrees at American Military University
Product recalls are an important aspect of reverse logistics. For adult learners who are interested in learning product recall management and related topics, American Military University (AMU) offers two degrees:
- An online Bachelor of Arts in Reverse Logistics Management
- An online Master of Arts in Reverse Logistics Management
Taught by expert faculty members, courses in these programs include reverse logistics policies and procedures, technology in reverse logistics, and transportation economics. Other courses involve best practices in reverse logistics and reverse logistics management.
These degrees have also received specialty accreditation from the Accreditation Council for Business Schools and Programs (ACBSP®). For more information on these degrees, visit AMU’s business administration and management degree program page.
ACBSP is a registered trademark of the Accreditation Council for Business Schools and Programs.